Understanding the Principle of Nanoindenter for Material Testing
High temperature publications 2024
Application Notes
Measuring Hardness and Elastic Modulus with Nanoindentation - Micro Materials UK
The principle of a nanoindenter is based on nanoindentation, a technique used to measure the mechanical properties of materials at the nanoscale, such as hardness, elastic modulus, and creep. It works by pressing a sharp indenter into the surface of a material under controlled force while measuring the depth of the indentation.
How Nanoindentation Works:
- Indentation Process
- A sharp indenter, typically made of diamond, is pressed into the surface of the material at a controlled load. The force applied and the depth of indentation are precisely monitored throughout the process.
- Load and Displacement Measurement
- During the indentation, both the force applied and the displacement of the indenter are measured in real-time. This provides a load-displacement curve that can be used to derive key mechanical properties.
- Elastic and Plastic Deformation
- When the indenter penetrates the surface, it causes both elastic deformation (reversible) and plastic deformation (permanent). The ratio of these deformations helps determine the material's hardness and elastic modulus.
- Continuous Stiffness Measurement (CSM)
- Some advanced nanoindenters use continuous stiffness measurement (CSM), where the rate of indentation is periodically paused to measure the stiffness of the material by analyzing the response of the material to small oscillations. This allows for the measurement of both hardness and elastic modulus without needing separate tests.
- Data Analysis
- The load-displacement curve obtained during testing is analyzed to extract mechanical properties:
- Hardness: The maximum depth of indentation or the force-to-area ratio.
- Elastic Modulus: The slope of the unloading curve.
- Other Properties: Depending on the type of test, properties like creep resistance, strain rate sensitivity, or friction can also be measured.
- The load-displacement curve obtained during testing is analyzed to extract mechanical properties:
For immediate assistance, you can reach us by phone or email. Our team is always happy to answer any queries you have, big or small. Check our contact details below:
- Phone: +441978261615
- Email: info@micromaterials.co.uk
- Office Address: Willow House • Yale Business Village • Ellice Way • Wrexham • LL13 7YL • United Kingdom
- Business Hours : We operate from 08:30am to 05:00pm Monday through Friday, and we aim to respond to all messages within 24 hours.
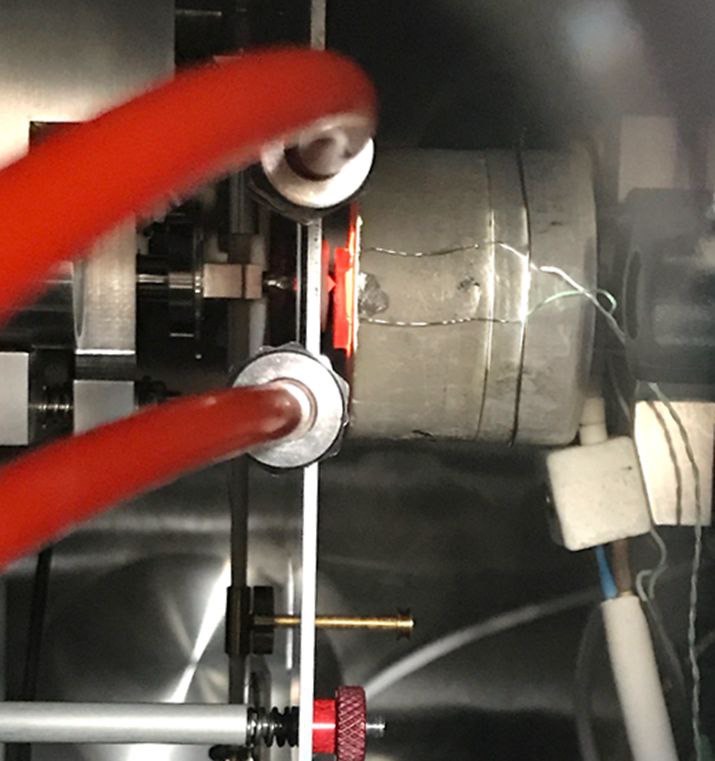
Inside a NanoTest Xtreme nanomechanical test system, capable of testing at high temperatures, upto and exceeding 1000 °C , under high vacuum conditions
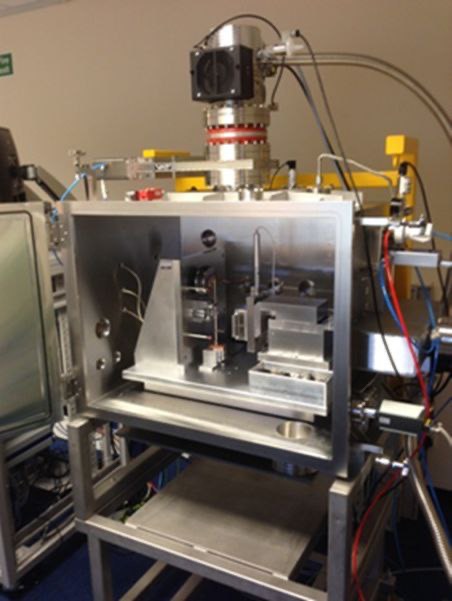
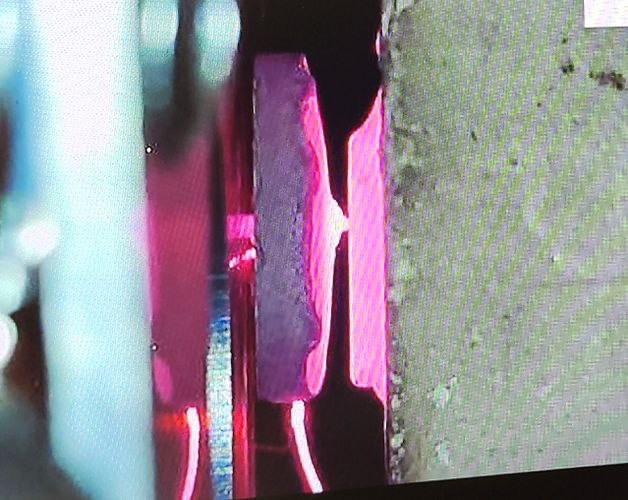
Image showing high temperature nanoindentation testing at temperatures over 900 °C using the NanoText Xtreme instrument supplied by Micro Materials Ltd
Image taken by Adrian Harris of Micro Materials Ltd, showing localised heating at 950 °C on an Xtreme system
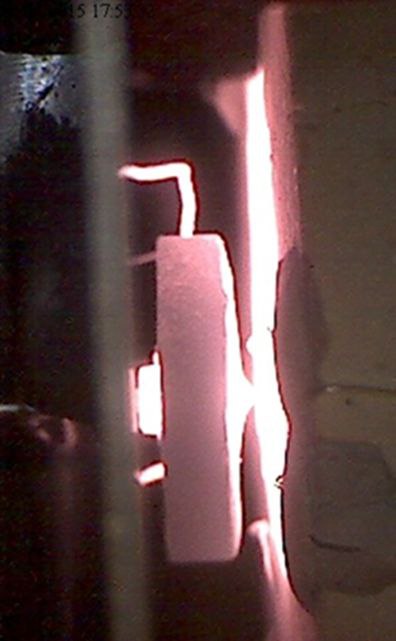
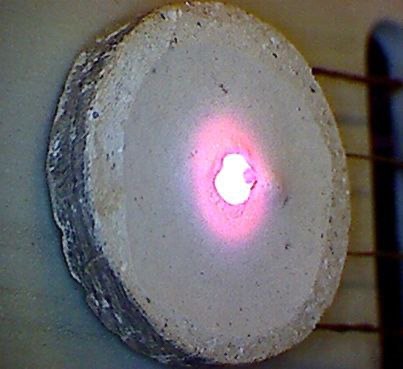
Image taken by Andrew Bird (Micro Materials Ltd), showing localised heating at
750 °C on an Xtreme system in use at the University of Oxford
Nanomechanical testing to 1000 °C
Application Notes
High temperature micro-scratch and impact
Technical Notes
High temperature creep resistance
Application Notes
Nuclear materials
Application Notes
Explore More
To further enhance your experience and understanding, we invite you to check out the following pages on our website that we believe are essential to your journey with us:
- High-Temperature Nanoindentation Testing for Advanced Material Characterization
- Advanced Nano Scratch and Wear Testing for Coatings and Materials
- Nano-Impact Testing for Advanced Material Performance in High-Stress Applications
These pages offer valuable insights and resources to help you achieve your goals.