High-Temperature Nanoindentation Testing for Advanced Material Characterization
NanoTest High temperature nanomechanical measurements portfolio
Application Notes
Unlocking Material Performance with High-Temperature Nanoindentation Testing
The mechanical properties of materials are almost without exception, strongly temperature dependent. Many major advances in technology have been achieved by developing materials which can offer sufficient performance at greatly elevated temperatures, classic examples being superalloys which are key to modern jet aviation, cutting tools for high speed machining, and materials for current and future energy generation including nuclear fusion.
All these examples have one thing in common and that it that the mechanical properties are achieved through nanometre to micron length scale materials science. Microstructural design and control, surface modifications, and the use of thin PVD and CVD coatings are all commonly used technologies to achieve specific objectives. In order to fully understand and accelerate development, the ability to study these small-scale features and structures at application specific temperatures is essential.
The NanoTest™ Vantage™ offers the researcher an unrivalled suite of high temperature testing capabilities including indentation, scratch and wear testing, impact testing and small scale tribological techniques.
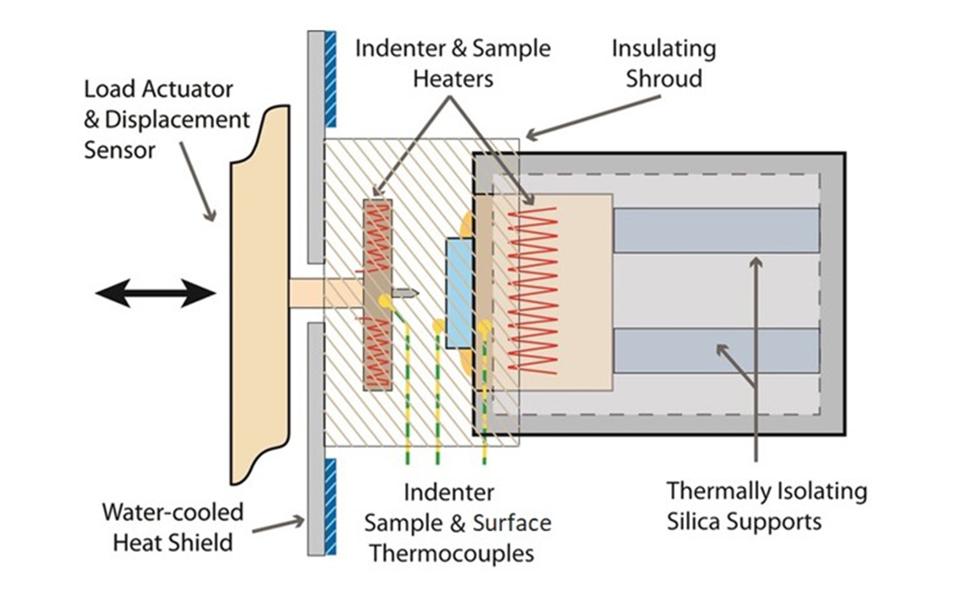
Low thermal drift
Independent heating of the sample and the indenter is essential in achieving low rates of thermal drift. The hot zone is thermally isolated from the rest of the instrument to minimise the time between starting heating and staring testing. Sensors are located well outside of the path of convected or radiated heat contributing greatly to the inherent stability of NanoTest™ instruments at elevated temperature.
A sample mounting area of 16 x 16 mm2 is available, allowing larger or multiple samples to be mounted and tested at once.
Both the sample and indenter are actively and independently heated to achieve isothermal contact and the best possible methodology for elimination of thermal drift and thus the most reliable test data.
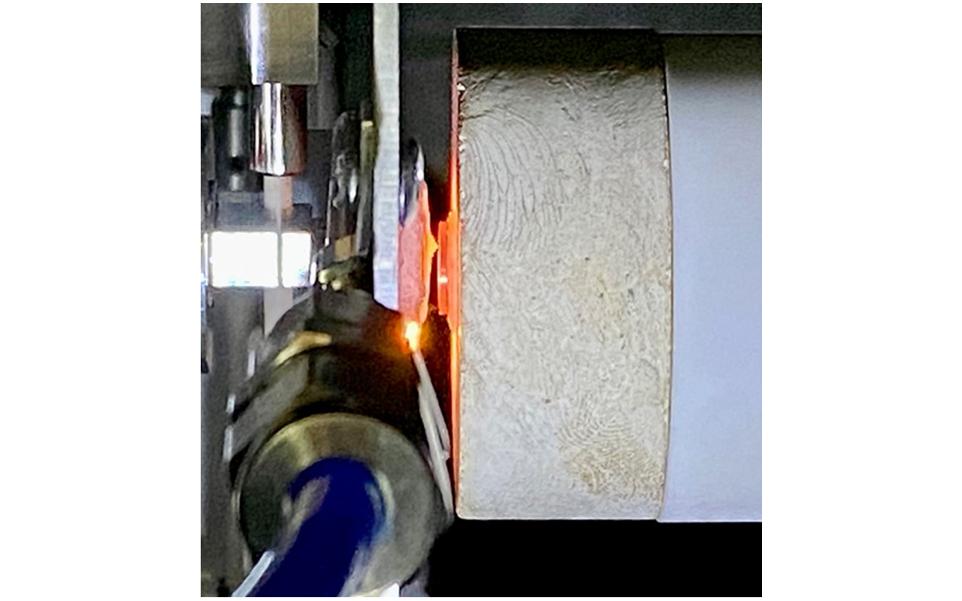
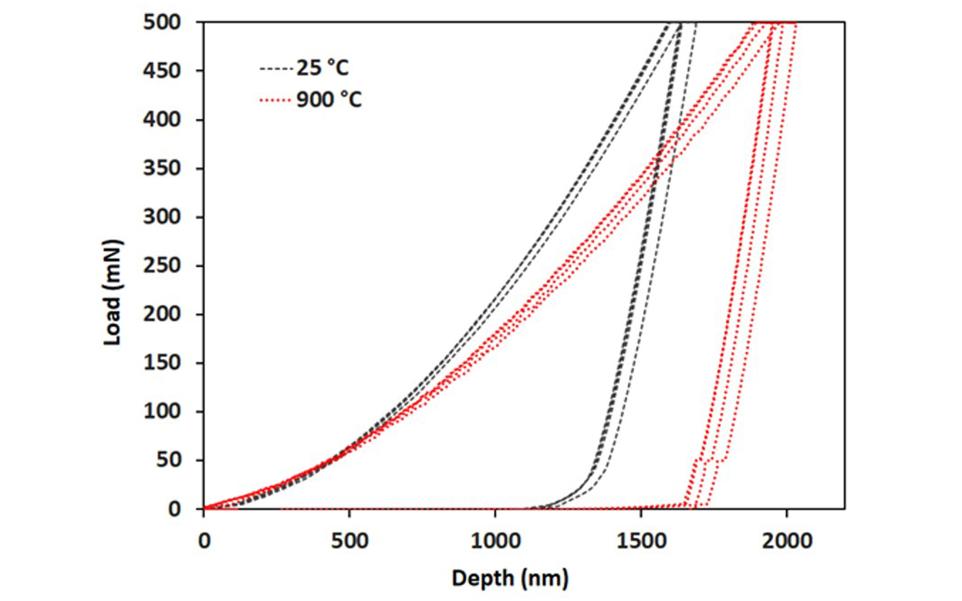
Inherent thermal stability
The inherent thermal stability of NanoTest™ instruments, along with patented temperature control methodologies and highly flexible experiment design possibilities make it the go-to solution for elevated temperature nanoindentation.
A wide range of indenter materials is available to allow testing of almost any material. In this example the sample material is tungsten which will dissolve a diamond indenter at elevated temperature. Instead, a c-BN indenter is used.
All test modes - indentation, scratch / wear, and impact testing are possible at elevated temperature
This allows high temperature property characterisation and the lab-scale replication of the widest range of real-world contact conditions.
Examples are detailed in this e-reader product brochure: NanoTest high temperature nanomechanical measurements portfolio.
This example focuses on the responses of two cutting tool coatings to repetitive impact at 300 °C and 600 °C. Prediction of temperature-dependent behaviour from room temperature data can be unreliable and testing at application specific temperatures can greatly accelerate material development.
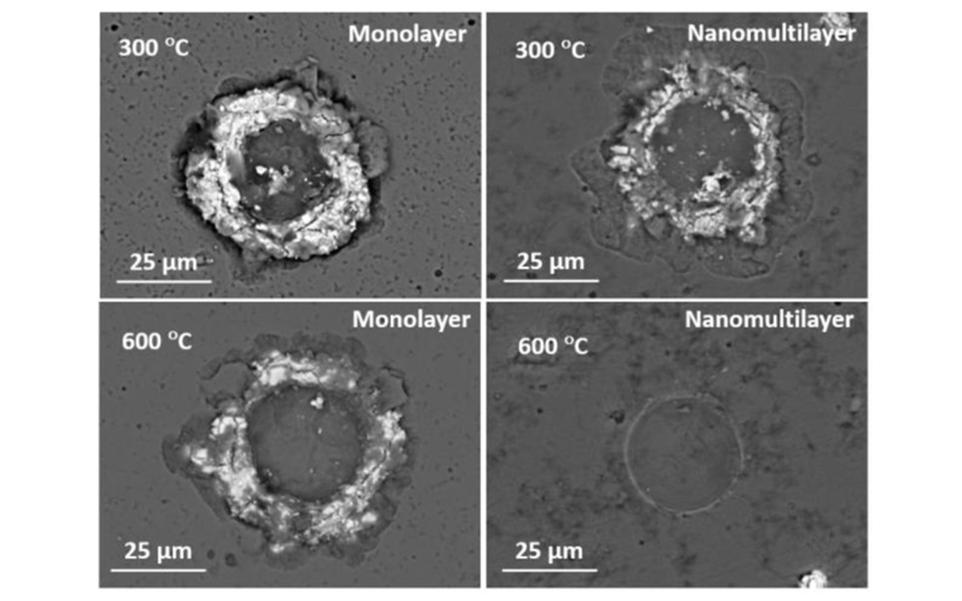
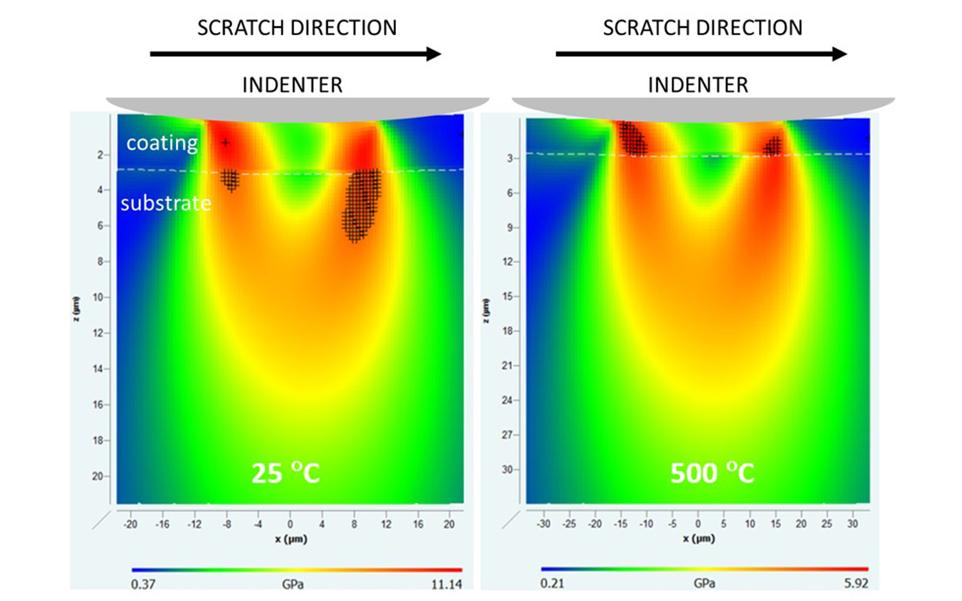
Scratch testing at application specific conditions can reveal major differences in how material systems respond to highly loaded sliding contact versus room temperature.
The NanoTest™ Vantage™ software is able to directly interface with a suite of packages from Saxonian Institute of Surface Mechanics. In this example Von Mises stress distributions maps have been created using output data from nanoindentation and nano-scratch tests from a NanoTest™ Vantage™. Note how the overloaded zones shifts from the substrate at room temperature to the coating at 500 °C. This helps us understand the differences in failure modes as temperature increases.
Nanomechanical testing to 1000 °C
Application Notes
High temperature micro-scratch and impact
Technical Notes
High temperature creep resistance
Application Notes
Nuclear materials
Application Notes
High temperature publications 2024
Application Notes
Explore More
To further enhance your experience and understanding, we invite you to check out the following pages on our website that we believe are essential to your journey with us:
- High-Temperature Nanoindentation Testing for Advanced Material Characterization
- Advanced Nano Scratch and Wear Testing for Coatings and Materials
- Nano-Impact Testing for Advanced Material Performance in High-Stress Applications
These pages offer valuable insights and resources to help you achieve your goals.