Acoustic Emission Monitoring for Nanomechanical Testing | Micromaterials
Acoustic emission
Technical Notes
Benefits of Acoustic Emission in Nanomechanical Testing
High frequency Acoustic Emission monitoring during nanomechanical tests such as nanoindentation, nano-scratch, nano-impact, micro-pillar compression and micro-cantilever bending provides valuable additional information to improve our understanding of material behaviour at the nano-scale.
Acoustic waves emitted during mechanical tests at the nano and micro scale are a rich source of information about the deformation behaviour (e.g. initiation and propagation of cracks, plastic instabilities, etc.) that may be otherwise inaccessible.
Benefits of the NanoTest™ Acoustic Emission module include:
- Improved accuracy in scratch test critical load
- Uncover cracking events in nanoindentation where load-depth profiles are smooth
- Differentiate between slip and fracture in impact
- Study yield behaviour
- Differentiate between different cracking processes
- Improved understanding of nanotribological tests
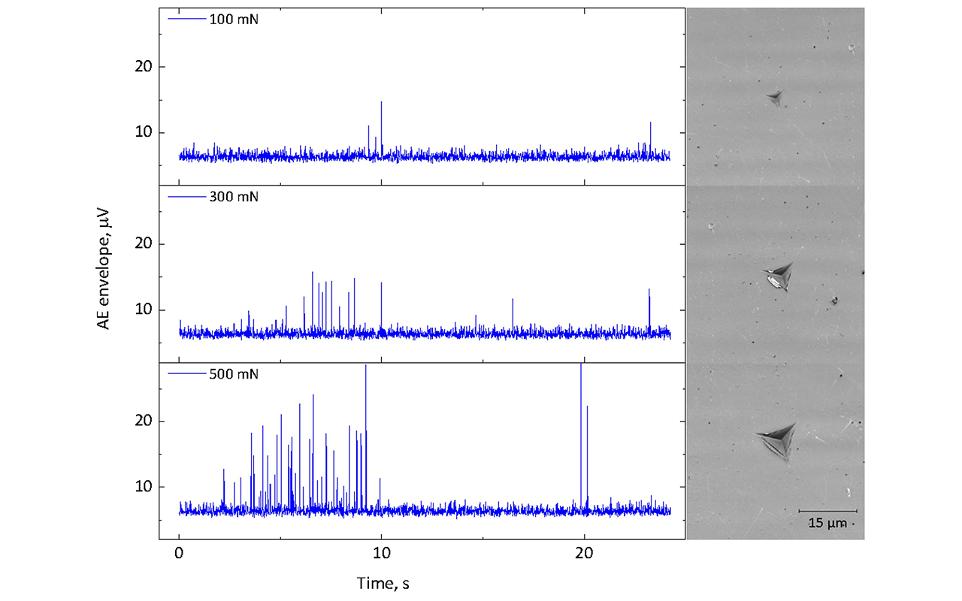
In nanoindentation of brittle solids cracking can occur. AE monitoring provides an effective method to study this even when there are no features seen on the indentation curves.
In 500 mN nanoindentation testing of fused silica with a Berkovich indenter there are no features on the loading curve to indicate cracking but as ISO 14577 notes, cracking typically occurs from 75-100 mN. AE monitoring shows discrete bursts of AE during loading and additionally during unloading from higher loads.
AE envelopes for fused silica indentation at 100, 300 and 500 mN (loading time = 10 s, hold at peak load before unloading = 5 s)
Acoustic Emission monitoring can be used to study pop-in events.
The figure shows spherical indentation of a model bcc material (Fe3Si single crystal). In the elastic regime (red line, Hertz fit) there is no AE but when activation of slip and/or nucleation of dislocations occur they are accompanied by strong AE signal (blue curve).
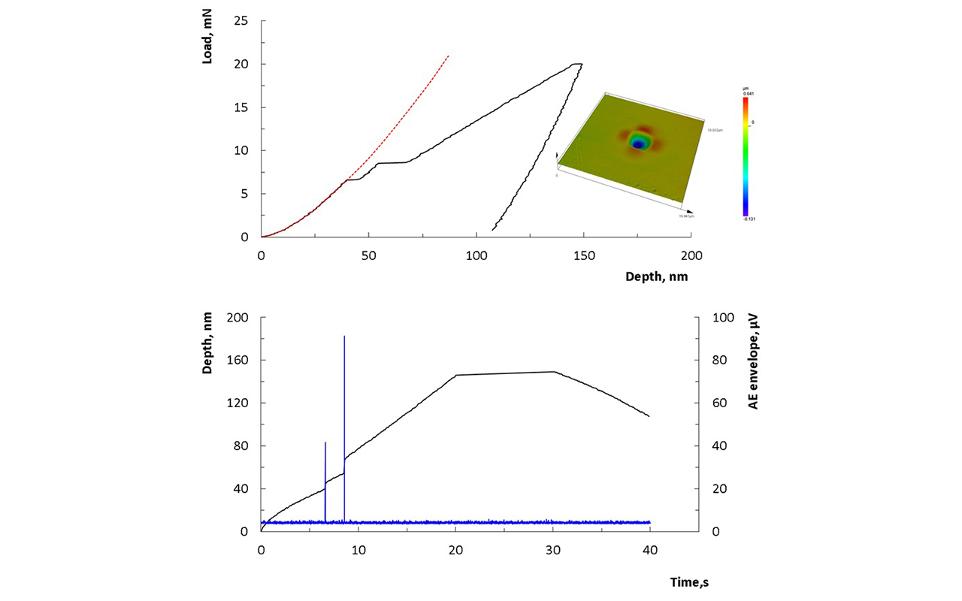
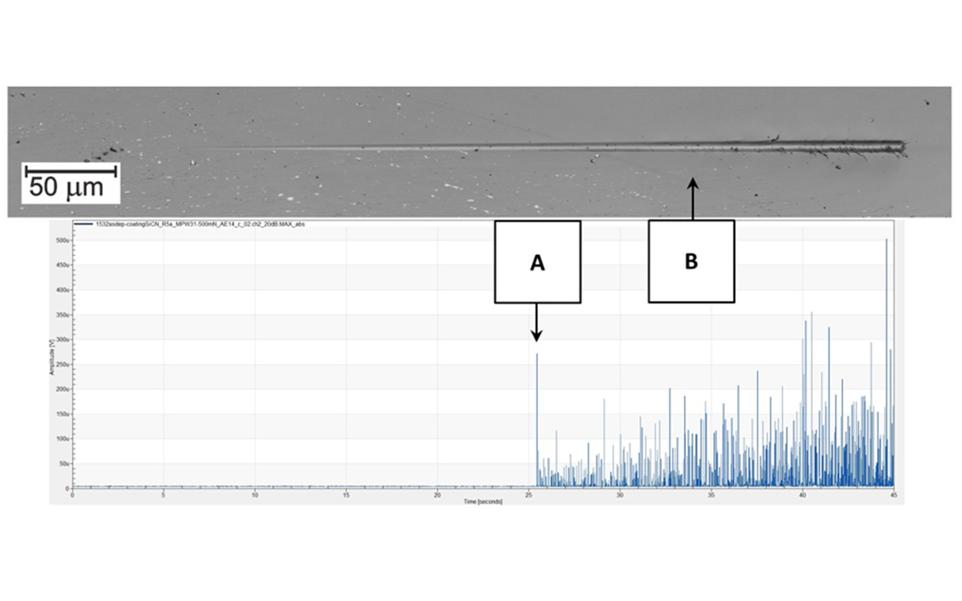
Acoustic Emission monitoring provides improved failure onset detection.
For example, when first cracks occur below the surface in a scratch test they are not visible and the critical load is incorrect.
A 500 mN nano-scratch test on 2.7 µm SiCN coating deposited using magnetron sputtering on silicon with a 5 µm diamond probe.
Strong AE is detected from the interface cracking at a lower critical load (point "A") than the first angular cracks which appear on the surface at point B. Focussed Ion Beam milling through the scratch track confirmed the cracking at point A.
Explore More
To further enhance your experience and understanding, we invite you to check out the following pages on our website that we believe are essential to your journey with us:
- High-Temperature Nanoindentation Testing for Advanced Material Characterization
- Advanced Nano Scratch and Wear Testing for Coatings and Materials
- Nano-Impact Testing for Advanced Material Performance in High-Stress Applications
These pages offer valuable insights and resources to help you achieve your goals.
References:
2. High frequency acoustic emission monitoring in nano-impact of alumina and partially stabilised zirconia, BD Beake, R Ctvrtlik, AJ Harris, AS Martin, L Vaclavek, J Manak, V Ranc, Mater Sci Eng A 780 (2020) 139159 (11pp).
Scratch and friction
Technical Notes
Nanoindentation
Technical Notes
High load testing to 30N
Technical Notes