Nano-Impact Testing for Advanced Material Performance in High-Stress Applications
Nano-impact and fatigue
Technical Notes
Enhance Material Durability with Precision Nano-Impact Testing for High-Stress Environments
Taking 5 mins or less, nano-impact tests provide a direct correlation to coating performance in applications involving repetitive contact, in metal cutting and in auto- and aero-engines. Cyclic nano-impact testing is commonly used to simulate high-speed machining. The strain rate in the impact test is much higher than in nanoindentation. Single impacts are used to study hardness at high strain rate. Random (statistically distributed) impact testing is used to simulate solid particle erosion.
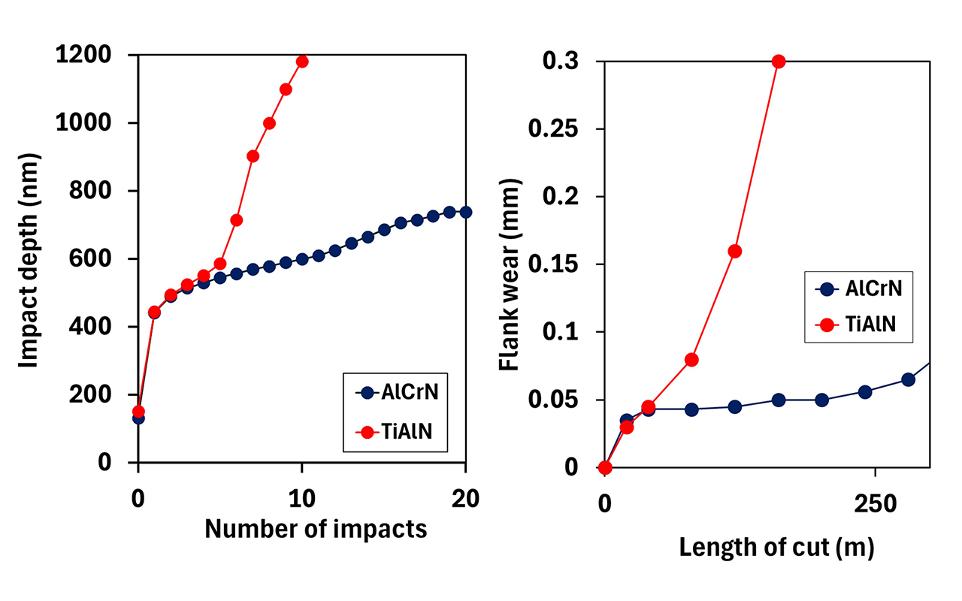
Comparative behaviour of AlCrN and TiAlN coatings in cyclic nano-impact tests with cube corner indenter and in end milling tests of AISI 1040 structural steel.
In the impact and cutting tests after the run-in there is a period of relatively low damage before a transition to a more severe wear mode and ultimately tool failure.
There is a clear correlation between the behaviour in the impact and cutting tests with AlCrN performing better in both.
Hard metals combine high hardness with high fracture toughness giving excellent wear resistance under highly loaded contact. In determining which carbide grade to use for a given application the fracture toughness or hardness alone may not be the best indicator of performance.
Impact tests on two cemented carbide grades with almost the same hardness. The carbide grade with lower % Co binder and lower fracture toughness showed improved damage tolerance in the micro-impact test. However, the grade with higher binder was susceptible to more severe impact damage matching its poorer performance in a drilling application.
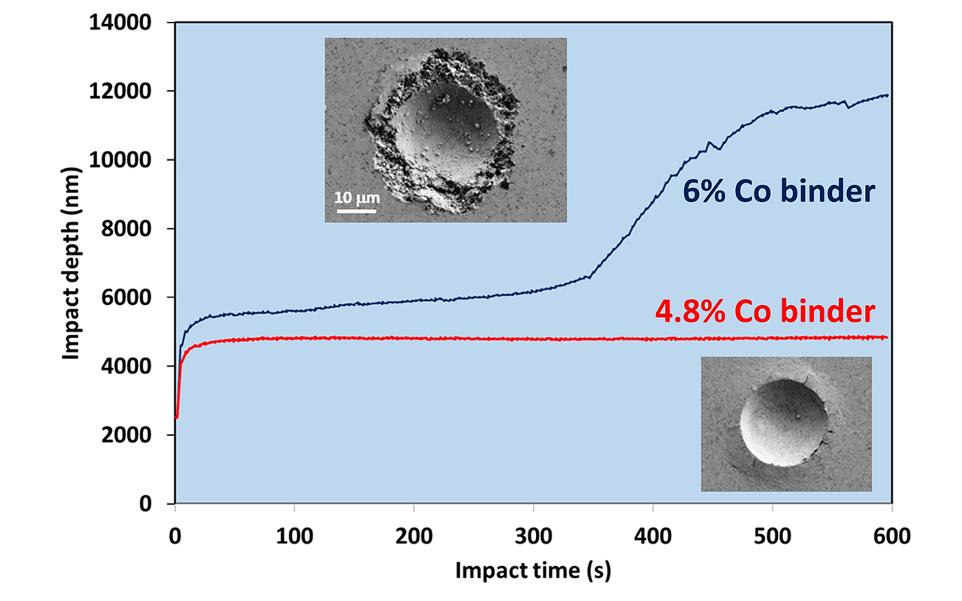
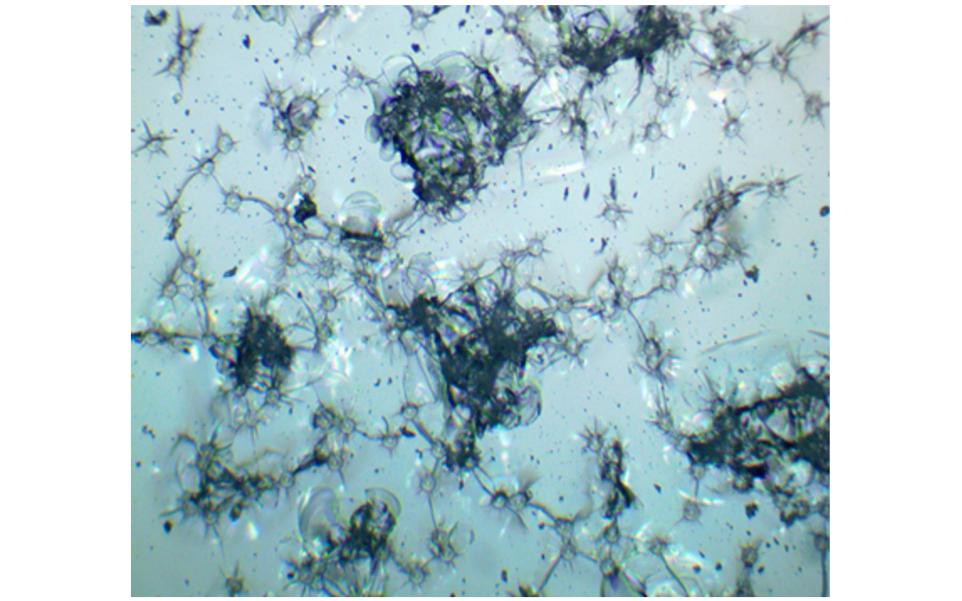
Spatially-distributed impact testing - 250 impacts on BK7 glass at 500 mN applied load using a 25 µm end-radius diamond conical probe in a rectangular distribution over a 500 µm x 500 µm area.
The radial-lateral crack system extends far from each impact causing crack systems between impacts to join up and increase the rate of material removal. Damage on fused silica was much lower under the same conditions consistent with its lower erosion rate.
Micro-impact testing
Technical Notes
Spatially-distributed impact
Technical Notes
Nano-impact testing of DLC coatings
Application Notes
High strain rate testing of aerospace composites
Application Notes
Wear resistant coatings
Application Notes
Impact Publications
Application Notes
Explore More
To further enhance your experience and understanding, we invite you to check out the following pages on our website that we believe are essential to your journey with us:
- High-Temperature Nanoindentation Testing for Advanced Material Characterization
- Advanced Nano Scratch and Wear Testing for Coatings and Materials
- Nano-Impact Testing for Advanced Material Performance in High-Stress Applications
These pages offer valuable insights and resources to help you achieve your goals.