Advanced Nano Scratch and Wear Testing for Coatings and Materials
Scratch and friction
Technical Notes
Precise Nano Scratch and Wear Testing for Enhanced Material Durability
The high lateral rigidity of the NanoTest™ Vantage™ system makes it particularly well suited to performing nano- and micro- scratch tests. In addition to simple ramped load scratches, multi-pass nano-scratch tests have been part of the NanoTest™ scratch module since 1991. The 3-scan procedure (topography scan – ramped load scratch - topography scan) described in CEN 17627 [1] enables identification of failure mechanisms, such as the role of stress, in more detail.
With the 30 N head it is possible to perform micro-scratch tests to study thicker coatings and also investigate the influence of hardened sub-layers on scratch test critical loads and failure mechanisms.
In addition to the standard repetitive scratch tests where all the scratches are in the same track, our novel randomised nano-scratch test technique involving statistically distributed parallel scratches has been developed to more closely simulate abrasion.
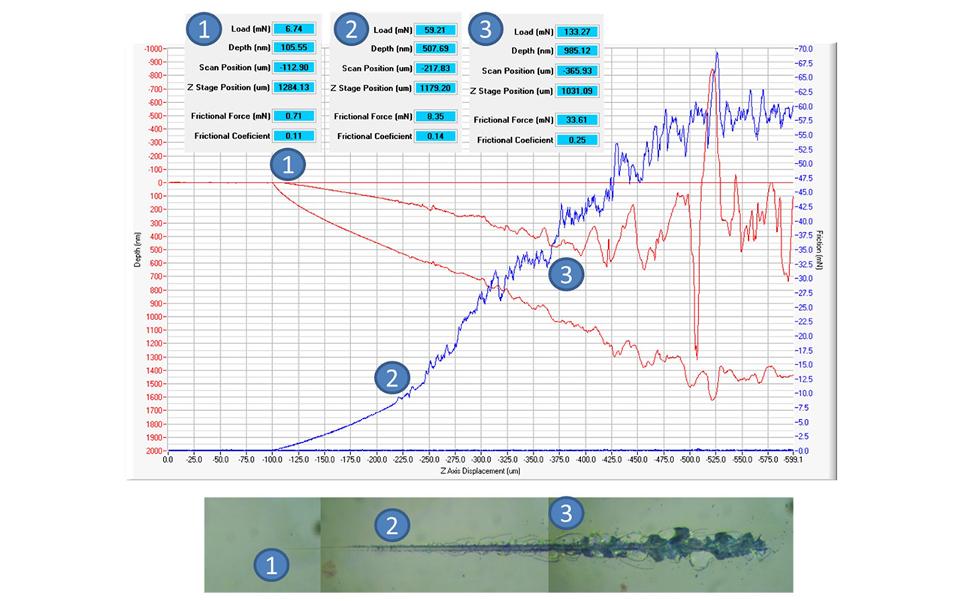
3-scan nano-scratch tests on 80 nm PVD ta-C coating on glass with a 3.8 µm probe. 1 = yield 2 = coating cracking 3 = total failure. The hard coating yields at low load despite having high H3/E2 due to plastic deformation of the much softer glass substrate. By removal of the instrument compliance contribution to the measured deformation the true nano-scratch and nano-wear depth data are displayed after levelling [2,3].
Ramped load micro-scratch test on 2 µm TiN PVD coating with high surface roughness on D2 tool steel.
Test performed as 3-pass topography-scratch-topography test with a R = 25 µm radius spherical diamond indenter.
1 = critical load for chipping 2 = total coating failure
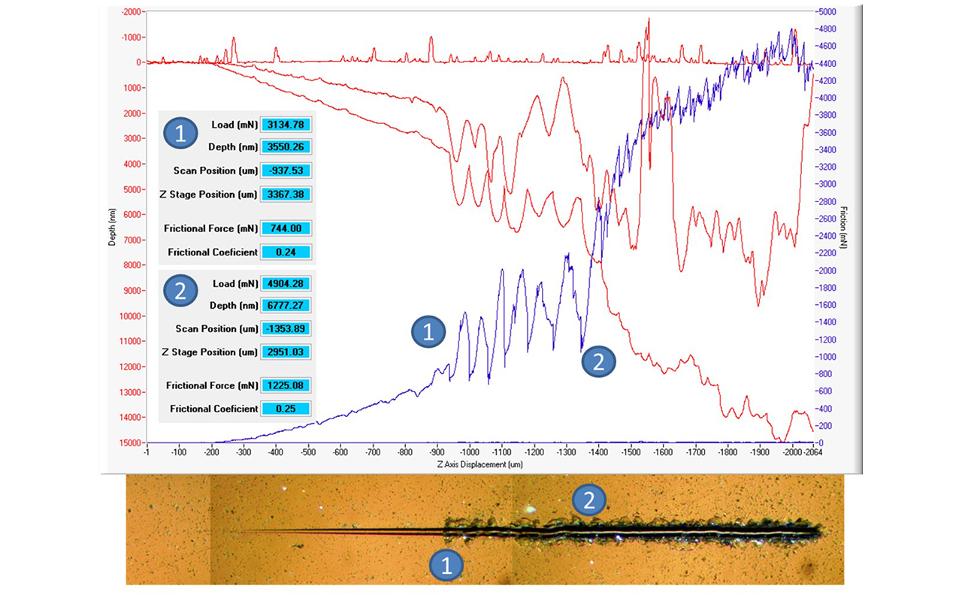
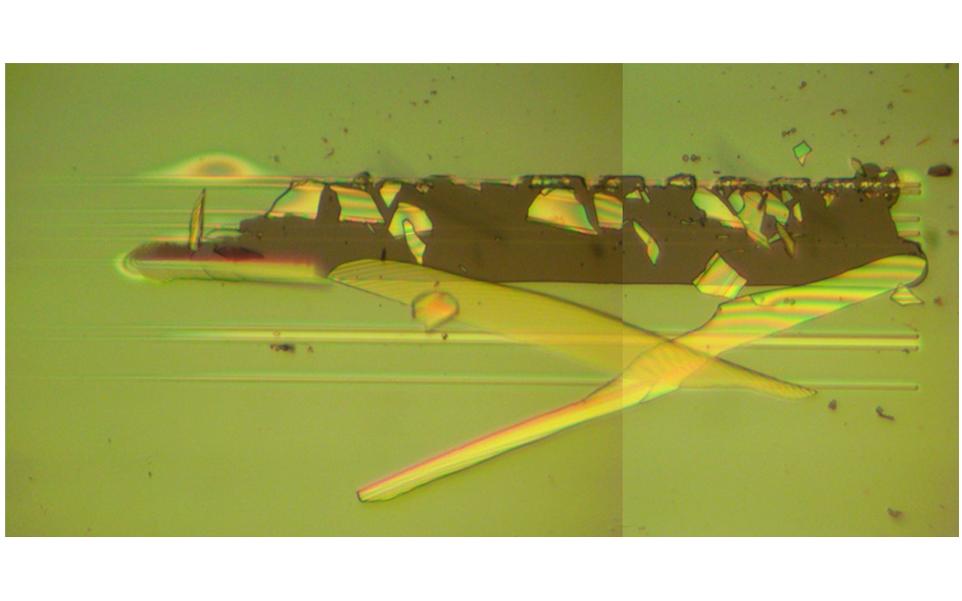
Randomised (statistically-distributed) nano-scratch test
Our novel randomised (statistically distributed) nano-scratch test technique has been developed to more closely simulate abrasion [4]. It’s a unique tool to help design more damage-tolerant materials.
Wear development is monitored cycle-by-cycle to provide deeper understanding of failure mechanisms in coatings and bulk materials.
The technique provides greater sensitivity to weak coating adhesion than a standard nano-scratch test – the figure shows obvious failure of an optical coating deposited on a non-clean substrate.
References:
1. CEN/TS, 17629:2021 Nanotechnologies — Nano- and micro- scale scratch testing (2021).
2. BD Beake, VM Vishnyakov, R Valizadeh, JS Colligon, Influence of mechanical properties on the nanoscratch behaviour of hard nanocomposite TiN/Si3N4 coatings on Si, J Phys D: Appl Phys 39 (2006) 1392-1397.
3. BD Beake, AJ Harris, TW Liskiewicz, Review of recent progress in nanoscratch testing, Tribology 7 (2013) 87.
4. BD Beake, VM Vishnyakov, SR Goodes, AT Rahmati, Statistically distributed nano-scratch testing of AlFeMnNb, AlFeMnNi and TiN/Si3N4 thin films on silicon, J Vac Sci Technol A 42 (2024) 013104.
High load testing to 30N
Technical Notes
Acoustic emission
Technical Notes
High temperature micro-scratch and impact
Technical Notes
Wear resistant coatings
Technical Notes
Explore More
To further enhance your experience and understanding, we invite you to check out the following pages on our website that we believe are essential to your journey with us:
- High-Temperature Nanoindentation Testing for Advanced Material Characterization
- Advanced Nano Scratch and Wear Testing for Coatings and Materials
- Nano-Impact Testing for Advanced Material Performance in High-Stress Applications
These pages offer valuable insights and resources to help you achieve your goals.